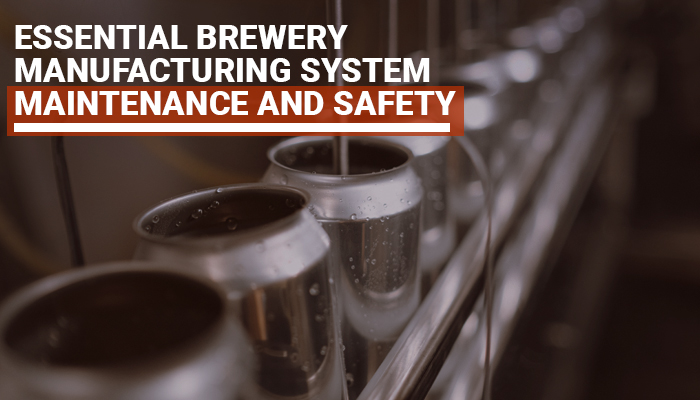
There are several important things to consider if you want your brewery manufacturing business to succeed. Aside from using specialized ingredients, staff working in the facility must follow strict temperatures throughout the brewing process and be cautious of caustic chemicals that are dangerous if proper care is not observed. A well-maintained machinery is vital since the brewery contains brewing equipment and systems such as malt mills and fermentation tanks that operate for long hours.
Everyone in the brewery manufacturing industry must observe the highest level of safety. You must be careful when running specialized machinery and chemicals can be sensitive to extreme temperatures. The brewing process can be quite dangerous. Working inside a brewery manufacturing facility can put employees at risk if these hazards are overlooked or neglected. To ensure that a brewery manufacturing business runs properly and safely, here are 8 maintenance and safety considerations that must be followed at all times.
8 Maintenance And Safety Tips For Brewery Manufacturing
1. Clean the Inside of the Tank.
Always maintain a regular cleaning schedule inside the brewery manufacturing plant. The brewing process is continuous which can scale the equipment and the thermal conductivity is lost. All these can affect the beer so cleaning the inside of the tank is important to prevent such problems from happening. Use a nitric acid-based cleaner when cleaning the inside of the tank to remove the scale. Oxidants can help eliminate stubborn deposits on stainless steel. Use hot water to flush the caustic alkali inside the pipes. Softer metals are preferable for scrubbing if you are doing manual cleaning.
2. Implement Spare Parts Management.
The spare parts management system can provide production efficiency and safety in all brewery manufacturing. Use the ABC analysis method to easily classify the spare parts. Class A is a critical spare part that must have enough stocks in the brewery so you can immediately replace and use it again. Class B are spare parts of general importance. Make sure that your brewery equipment suppliers have stocks that can be delivered on short notice. Category C are non-critical spare parts that can be delivered by brewery equipment manufacturers even after several weeks. Always check your brewery manufacturing equipment to identify problems and make necessary solutions.
3. Boiler Maintenance.
Many brewers use steam boilers when they buy brewery equipment. The steam boiler is a very powerful tool but most people do not know how it works. Improper maintenance of the steam boiler can cause the equipment to malfunction or get damaged. When this happens, it can be very expensive for a brewery manufacturing business. To maintain and make it functional again, repair your steam and condensate leaks. Using city water rich in oxygen and chlorine as condensate can help avoid boiler rot.
4. Forklift and Pedestrian Safety.
Brewery manufacturing employees work around the moving forklift daily. They are used to seeing it that they may sometimes let their guard down and neglect precautionary measures. To avoid accidents, develop and implement a complete workplace transportation safety plan inside the facility. Measures include:
- Use clear signs and floor markings to separate forklift and pedestrian traffic routes.
- Install physical barriers.
- Improve visibility inside the brewery manufacturing facility by using reflective tapes and highly visible reflective vests.
- Ensure that audible reverse alarms and lights on all forklifts are functioning well.
5. Heat and Fire Safety.
Large flames are needed to boil lots of water when starting the brewing process. Despite there are standard safety precautions, working with flames is still dangerous. A modified lockout/tagout system must be used to make sure the burners are not turned on when employees work near the burners. A brewery manufacturing plant must implement safety precautions to ensure that the water does not spill on the employees or they do not fall into the containers if they are working close to these when the water is being boiled.
6. Slip and Fall Hazards.
Volumes of liquid are being moved inside the brewery manufacturing facility daily. Water and beer can easily spill due to a dropped bottle, leaky hose, or a missed pour. The spills can leave the floor wet and slippery causing accidental slips and falls. To help minimize these risks, a brewery must install anti-slip floor tape, grated floors, and other safety equipment so everyone can keep their balance.
7. Keg Safety.
Beer is often put into kegs where it is stored until its delivery to a bar or other consumer. Although kegs are generally safe, they can cause serious damage when accidents suddenly happen. Keg can explode if it is over-pressurized so you must monitor its pressure levels. Ensure that all kegs inside the brewery manufacturing facility are in good condition to keep everyone safe.
8. Pipe and Hose Labeling.
A brewery manufacturing plant has several pipes that bring water to certain areas, move the beer during the brewing process, and assist with the bottling. It is for the safety of all employees that they must identify what each pipe is and where it is going. A pipe labeling strategy must be in place to keep everyone safe. Someone might accidentally open a pipe expecting beer to flow out which turns out to be hot water instead can cause serious burns.
ALSO READ: Different Types of Industrial Machine Maintenance that Must be Done Regularly
A brewery manufacturing facility must ensure that all its machines are well-maintained for the smooth flow of its operations. The last thing you would like to happen to a piece of equipment when brewing beer is to suddenly stop working which may cause downtime and affect the productivity of the business. A regular maintenance check-up of machines is important to identify problems and address them immediately. Safety measures are essential within the brewery manufacturing plant. Workers can be put at risk from hazards such as slippage, serious burns, and explosions, among others.
For more than four decades, Hayama Industrial Corporation (HIC) has been a trusted name in the manufacturing and fabrication industry in the Philippines. Among its reliable services include Rehabilitation & Equipment Installation which are used for different production lines. Hayama helps several businesses maintain and operate their processing systems from installation to maintenance and rehabilitation to ensure their business growth and success. Do you want to install specialized equipment in your manufacturing business and want help in its proper maintenance? Hayama can assist.
Recent Comments